Medical bottle cap Solution
Jeepine Pharmaceutical Closure Production Solutions
1. Overview of Pharmaceutical Plastic Closures
Pharmaceutical plastic closures are essential components designed for use with pharmaceutical plastic bottles. These closures often come into direct contact with medication and play a critical role in providing gas barrier properties, moisture resistance, and protection against contamination. They effectively prevent the egress of contents from the bottle while simultaneously preventing the ingress of foreign substances.
2. Classification of Pharmaceutical Closures
Pharmaceutical closures are predominantly integrated types, primarily made of plastic materials, combining multiple functionalities. The main categories of integrated closures are as follows:
Integrated Tamper-Evident Closure (TEC): Also known as a pilfer-proof cap. It features an added skirt (tamper-evident ring or band) connected by breakable bridges at the base of a standard threaded closure. Upon unscrewing, the band's ratchet teeth engage with the bottle's locking ring. Reverse rotation causes the band to break and detach. The intact band upon first opening indicates that the package has not been previously opened or tampered with. The required opening torque should be designed to be light and moderate for smooth band detachment.
Integrated Desiccant Closure: Incorporates a desiccant within the closure body to significantly reduce moisture ingress during product usage. Widely adopted in the industry.
Integrated Shock-Absorbing Closure: Designed to protect fragile items like capsules from damage due to shaking by integrating cushioning elements into the closure base.
Integrated Easy-Open Closure: Features an added mechanism to assist users in opening the closure.
Integrated Branding Closure: Integrates branding elements (logos, trademarks) directly onto the closure.
Integrated Dispensing Closure: Incorporates a metering device for controlled dosage dispensing.
Integrated Safety Seal Closure: Combines a one-time breakable seal system into the closure, preventing bottle reuse after initial opening to ensure product integrity.
3. Working Principle of Pharmaceutical Closure Making Machine
The pharmaceutical closure making machine independently developed by Jeepine Intelligence employs a fully automatic compression molding process. Utilizing high-speed rotary compression molding with multiple upper and lower molds, it produces various plastic closures for water bottles, pharmaceuticals, daily chemicals, and liquor bottles. The process: Granular plastic raw materials (e.g., PE, PP) are melted at high temperature and extruded quantitatively. The extrudate is cut into preforms by a cutter wheel and distributed evenly into individual mold cavities. The closures are then formed under pressure within the cavities.
4. Core Advantages of Jeepine's Pharmaceutical Closure Making Machine
Jeepine Intelligence provides superior pharmaceutical closure solutions, meeting critical performance requirements such as gas barrier, moisture protection, contamination prevention, and content retention, while also supporting customized closure designs and sizes. Furthermore, Jeepine's machines offer these distinct advantages:
Stable Operation: Integral turret design, high-precision dual-pump hydraulic system, PID-controlled low-pressure mold closing and high-pressure molding ensure reliable and stable running.
High Efficiency: Advanced high-speed feeding system, continuous high-speed rotary compression with multiple molds, vacuum-assisted cap ejection deliver outstanding productivity.
Energy Saving: Polymer low-temperature melting technology significantly reduces heating and cooling energy consumption.
Material Saving: Intelligent temperature-controlled extrusion, precise dosing and cutting of preforms, stable weight control, and optimized material utilization.
Operational Safety: Intelligent logic control system featuring automatic monitoring, alarm, diagnostics, and protection functions.
Hygienic Production: Enables integrated "Make-Closure / Blow-Fill-Seal" solutions. In-line closure production and conveying ensure a clean and hygienic process.
5. Your Ultimate Cap Solution: Comprehensive Compression Molding Line
Compact Footprint
Easy Maintenance, Safe Operation
Fully Automatic
Broad Process Window Flexibility
6. Six Core Systems of Guangzhou Jeepine Compression Molding Machine
Cap Compression System
Automatic Compression Molding Production
Automatic Cooling, Buffering & Unscrambling System
Rapid cooling, automatic cap orientation, enhanced stability and productivity.
Slitting System
Highly Accurate Hot-Slitting Technology
Printing System
Fully Automatic Printing, Superior Quality
Optical Inspection System
Online inspection with high-speed camera, automatic and accurate defect detection and ejection.
Packaging System
Automatic cap loading, infrared counting, minimizes manual contact and secondary contamination.
JeePine provides diversified cap solutions covering a wide range of industries such as food, beverage and pharmaceuticals:
Carbonated cap
Such as 2622 CSD CAP for carbonated beverages.
Static water cap
Such as 2622 WATER/CAF CAP, for purified water or mineral water.
Pharmaceutical caps
e.g. 28mm caps for pharmaceutical products.
Special application caps
e.g. white wine inner cap, toothpaste cap, etc.
Each solution specifies in detail the cap raw material (HDPE), bottle mouth size (e.g., 26mm, 28mm, etc.), sealing structure (inner stopper + outer stopper), weight (e.g., ranging from 1.1g to 6.9g), and application areas (e.g., carbonated beverages, water, fruit juices, dairy products, etc.), which allows for lightweighting, diversification, customization, and the development of new cap styles to ensure that we meet the various needs of our customers.
Recommended Solution
Cap Types Introduction
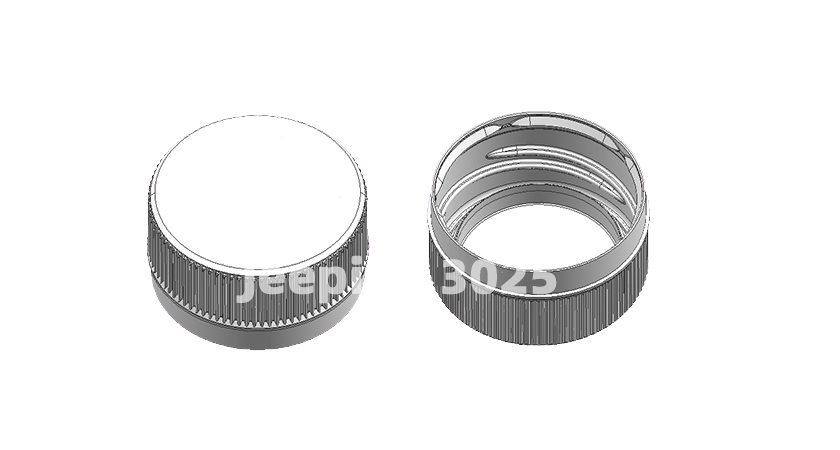
3025 WATER CAP
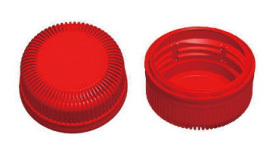
2622 CSD CAP
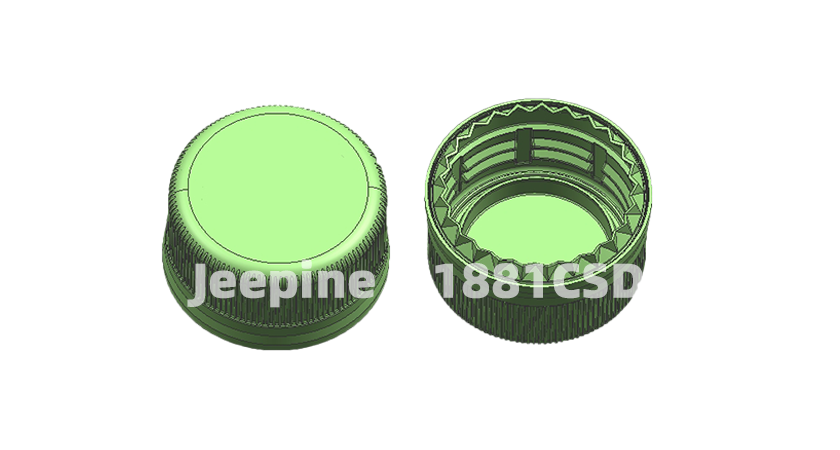
1881 CSD CAP
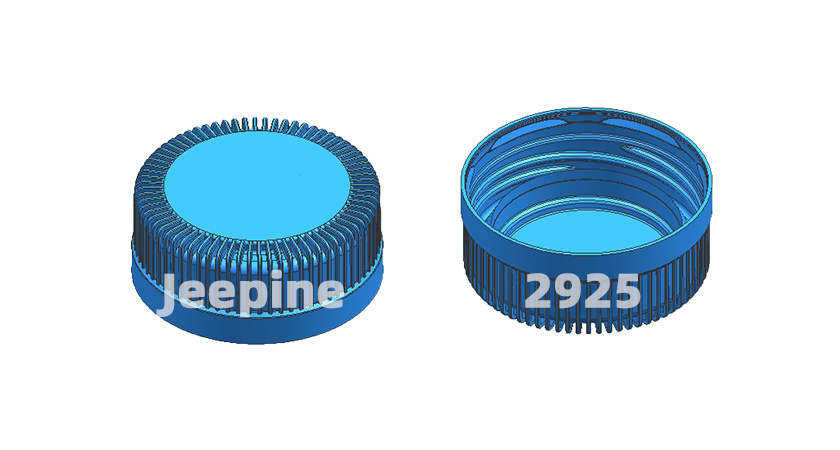
2925 WATER CAP